Project Details
Our most exciting and challenging project to date! Phase 2 of the Award Winning Seven Sisters rehabilitation project totalling 576m of 900mm SDR 26 PE 100 polyethylene liner installed over 2 pulls.
The Die Draw process was selected because it is it was uniquely suited to the challenging environment. Seven Sisters is a densely populated area with heavy traffic, restricted space, and a large number of underground utilities & services. The Die Draw process minimises installation size and footprint while maximising post-installation flow capacity. It was calculated that the increased bore size afforded by the tight fight liner provided an additional 5-million litres per day in pipe flow capacity when compared with alternative lining techniques.
The challenges faced in this phase were significant and for the second time on this project Die Draw Ltd had to find complex solutions and introduce new techniques never before seen in the industry. This project was the culmination of 7 months of engineering design and collaborations across multiple companies, agencies & industries.
Project details:
Client: | MorrisonWS |
Project: | Seven Sisters Phase 2 |
Location: | London |
Completion date: | 2022 |
Pipeline Length: | 576m |
Liner material type: | PE 100 |
Liner dimension: | 900mm OD, SDR 26 |
Host pipe: | 36” 150-year-old cast iron main |
Operating fluid: | potable water |
Operating pressure: | 4.2 barg |
PE 100 liner lifetime: | 100 years |
Challenges
As with Phase 1, this project faced considerable challenges. The primary design challenge with phase 2 was the close proximity of 2 other water mains (approximately 300mm apart) which meant there was not space to place the die adjacent to the the host pipe. In an industry first, Die Draw Ltd designed a complex solution that placed the die at street level and used heavy duty rollers to redirect the elastically reduced liner into the host pipe.



Other challenges faced with this phase
- Traffic management on and around one of London’s busiest roads
- Finding locations for launch and reception pits
- Determining space for welding and road closures for long strings of pipe
- Transferring winch load into a pipeline with ~300mm between adjacent live mains
- Transferring winch forces at an angle of 120° between adjacent pipes
- Cleaning the host pipeline of tuberculation
- Determining the ID of the host and any obstructions using camera and Lidar surveys
- Removal of obstructions prior to lining
- Transfer of liner under load from ground to pipe level using rollers
- Negotiation of a series of minor bends during the first insertion
Successful Outcome
Both pulls were executed with meticulous attention to detail, closely following the calculated loads, speeds, and designated timeframes. The entire liner pull-in process was completed without any deviations from the established plan. At Die Draw Ltd, we take great pride in our commitment to achieving consistent results, where projects are completed in strict accordance with specifications, devoid of unexpected events, and in full alignment with the original design, while taking into account all relevant variables.
Accomplishing such consistency in the execution of complex engineering projects underscores the substantial experience and expertise required to ensure a smooth and issue-free outcome.
The Die Draw method avoided the need for pipe replacement, which would have been very disruptive to homes and communities and have involved excessive road closures and noise pollution from construction work. Die Draw technology results in significant impact reduction to the community and environment as it requires less excavation and materials, decreasing carbon over the life of the scheme.
The Die Draw technology process significantly reduces the project cost and programme, while minimising disruption and maintaining the required flow requirements specified by the client.
Additional key achievements:
- Client benefitted from the lowest cost permanent works solution available to satisfy minimum bore requirements with a minimum 50 year design life for the fitted pipeline system
- Liner pipeline is fully structural meeting minimum bore requirements (and hence maximising flow capacity)
- Minimal traffic disruption and public inconvenience
- Safe transfer of 100T winch forces to avoid adjacent pipelines
- Low environmental impact
- Led to Phase 3 project continuation with installation early 2024
Gallery
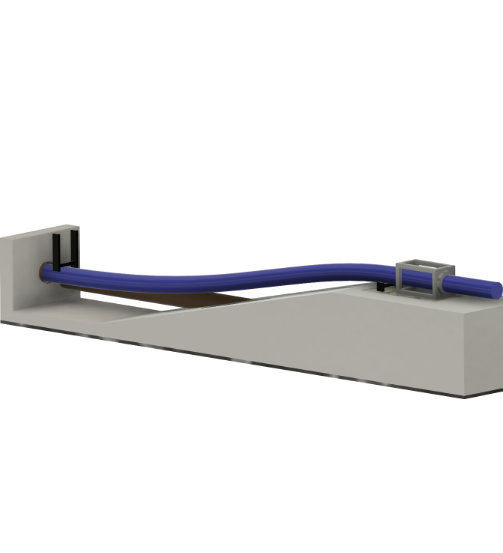
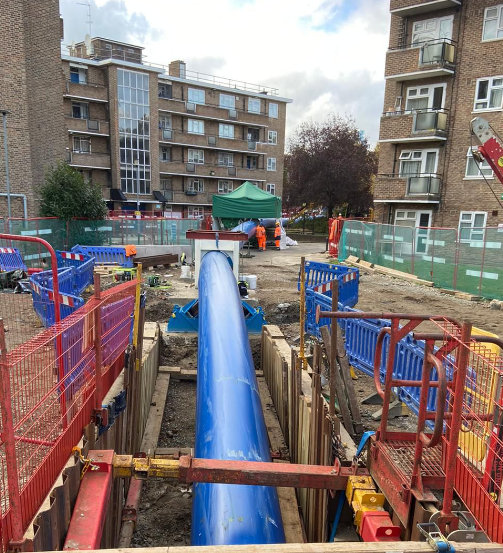
